Welding Equipment Market Innovations Driving Efficiency, Automation, and Sustainability in the Manufacturing Industry
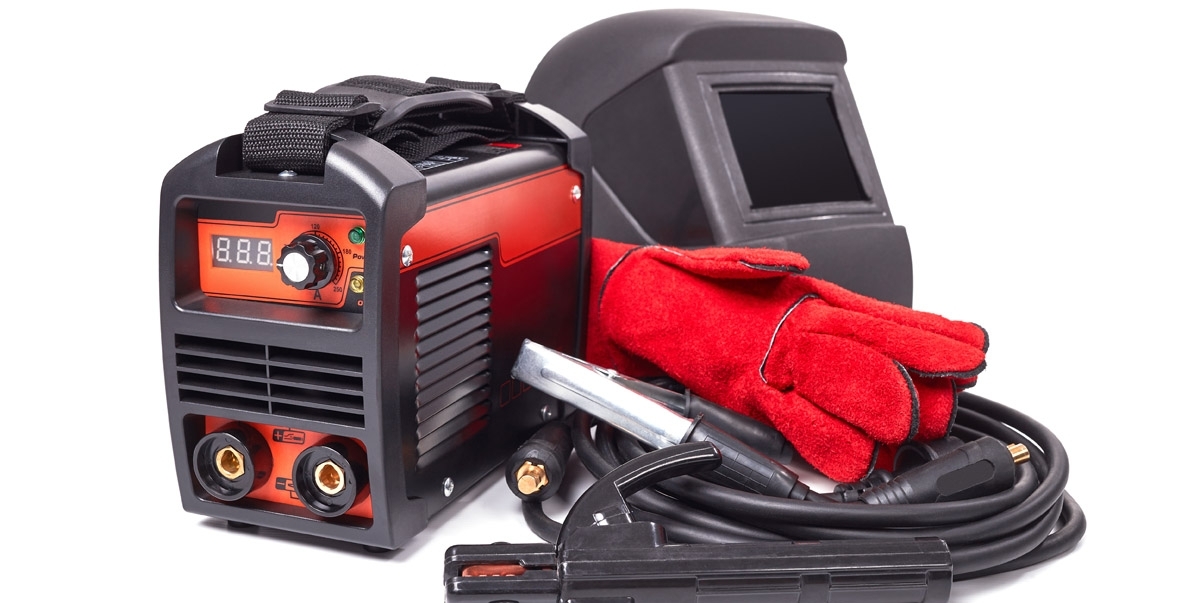
The welding equipment market is witnessing groundbreaking innovations that are redefining industrial fabrication and manufacturing processes. With technological advancements such as automation, robotics, and smart welding solutions, industries are experiencing increased efficiency, precision, and sustainability. The demand for modern welding equipment is being driven by the need for cost-effective, high-performance solutions that cater to diverse applications across automotive, aerospace, construction, and energy sectors.
Automation and Robotics Revolutionizing Welding
Automation is playing a crucial role in reshaping welding processes, offering improved consistency and efficiency. Robotic welding systems have become integral in industries requiring high-volume production with minimal human intervention. These systems enhance weld accuracy, reduce material wastage, and improve workplace safety by minimizing exposure to hazardous conditions. With advancements in AI and machine learning, robotic welding is evolving further, enabling real-time adjustments and adaptive welding capabilities for complex structures.
Smart Welding Technologies for Enhanced Performance
Smart welding technologies are becoming increasingly popular, integrating IoT and digital monitoring for precise control over welding parameters. These systems allow real-time data collection and remote diagnostics, ensuring optimal performance and reducing downtime. Cloud-based platforms enable seamless connectivity, offering predictive maintenance insights that help manufacturers prevent costly failures. Adaptive welding systems are also emerging, capable of adjusting to variations in material properties and environmental conditions, ensuring superior weld quality.
Advanced Welding Materials and Techniques
Innovations in welding materials and techniques are contributing to stronger and more durable welds. High-performance alloys, composite materials, and nanotechnology-based coatings are improving the longevity and strength of welded joints. Laser and friction stir welding are gaining traction, offering high-precision alternatives to traditional welding methods. These advanced techniques are particularly beneficial in aerospace and automotive manufacturing, where lightweight materials and structural integrity are critical.
Sustainable and Energy-Efficient Welding Solutions
Sustainability is becoming a key focus in the welding equipment market, with manufacturers prioritizing energy-efficient technologies. New-generation welding machines are designed to consume less power while delivering optimal output. The development of eco-friendly welding consumables, such as low-fume electrodes and recyclable shielding gases, is reducing environmental impact. Industries are also adopting hybrid welding techniques that combine multiple processes for enhanced efficiency, reducing waste and energy consumption.
The Future of Welding Equipment Market Innovations
The welding industry is poised for continuous transformation as technological advancements drive the development of more sophisticated solutions. The integration of AI, big data analytics, and augmented reality is expected to enhance training programs, improving workforce skills and productivity. As industries embrace Industry 4.0, welding equipment will become smarter, more connected, and capable of delivering unprecedented levels of precision and automation.

- Industry
- Art
- Causes
- Crafts
- Dance
- Drinks
- Film
- Fitness
- Food
- Jeux
- Gardening
- Health
- Domicile
- Literature
- Music
- Networking
- Autre
- Party
- Religion
- Shopping
- Sports
- Theater
- Wellness
- News