Understanding the Factors Behind Steel Rod Prices in India Today
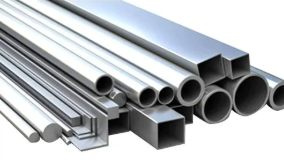
Steel rod are integral to India’s construction and manufacturing industries, and their pricing is influenced by a web of interconnected factors. From the cost of raw materials to regional variations and government policies, these elements shape the fluctuating steel market. Gaining insights into these dynamics can help stakeholders make informed purchasing and investment decisions.
Raw Material Costs: Iron Ore and Coking Coal as Key Drivers
The foundation of steel rod pricing lies in the cost of raw materials like iron ore and coking coal. These commodities are critical for steel production and are affected by global supply-demand dynamics, geopolitical events, and trade restrictions.
For example:
-
A surge in demand from major producers like China or supply chain disruptions can increase global iron ore prices, directly impacting steel production costs in India.
-
Similarly, coking coal prices, driven by energy market shifts, environmental policies, and mining regulations, can significantly affect production expenses.
These fluctuations in raw material prices directly influence the cost of steel rods in the market.
Domestic Demand: Construction and Infrastructure as Catalysts
India’s burgeoning construction and infrastructure sectors are the primary consumers of steel rods. Large-scale projects, such as urban housing initiatives, highways, and industrial development, drive substantial demand for steel products.
In periods of economic growth, heightened demand puts upward pressure on steel prices as manufacturers scale up production. Conversely, an economic slowdown reduces construction activity, leading to surplus supply and price stabilization.
Regional Variations: Transportation and Local Expenses
Steel rod prices exhibit regional differences across India, with metropolitan cities like Mumbai, Delhi, and Bangalore often experiencing higher costs. Key reasons include:
-
Transportation Costs: Regions far from steel manufacturing hubs incur higher logistical expenses, increasing the price of steel rods.
-
Local Taxes and Operational Expenses: Urban centers often have additional costs, such as higher storage fees and local levies, which further drive up prices.
Regions closer to steel plants or equipped with efficient transportation networks, such as parts of Odisha and Chhattisgarh, often benefit from more competitive pricing.
Conclusion
The pricing of steel rods in India is a dynamic interplay of raw material costs, domestic demand, regional variations, and production expenses. For consumers, contractors, and businesses, staying informed about these factors is crucial for effective decision-making in the steel market. As demand from construction and infrastructure projects remains robust, the need for continuous monitoring and strategic purchasing becomes even more critical.
If you are looking for best quality tmt bars, please visit our website : www.steeloncall.com or you can contact us through our toll-free number: 18008332929
#SteelRodPrices #SteelIndustryIndia #ConstructionMaterials #TMTBars #SteelMarket #InfrastructureDevelopment
- Industry
- Art
- Causes
- Crafts
- Dance
- Drinks
- Film
- Fitness
- Food
- الألعاب
- Gardening
- Health
- الرئيسية
- Literature
- Music
- Networking
- أخرى
- Party
- Religion
- Shopping
- Sports
- Theater
- Wellness
- News