The Impact of Core Cutting Line Efficiency on Transformer Manufacturing Costs
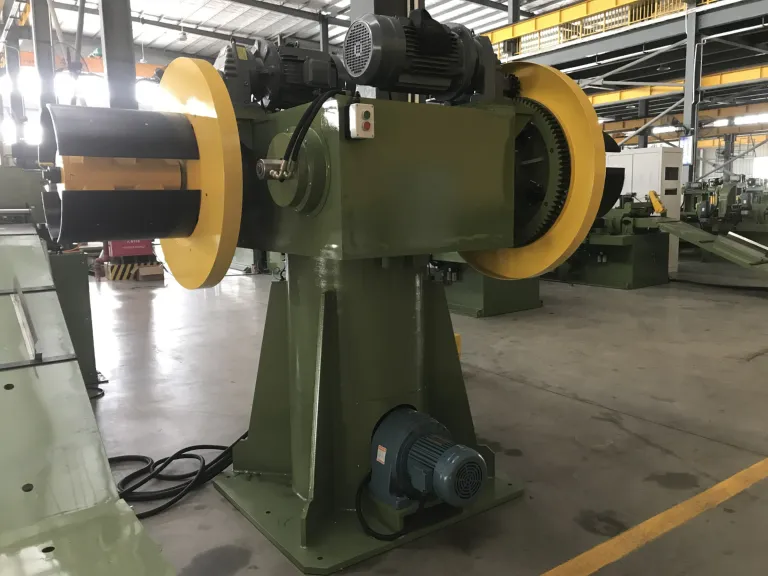
In the transformer manufacturing industry, efficiency is key to reducing costs and increasing productivity. One crucial aspect of the manufacturing process that significantly impacts efficiency is the core cutting line. The core cutting line is responsible for cutting and shaping the core materials used in transformer production. In this article, we will explore the impact of core cutting line efficiency on transformer manufacturing costs and discuss ways to improve efficiency, reduce costs, and increase productivity.
The Role of Core Cutting Line in Transformer Manufacturing
The core slitting machine is a critical component of the transformer manufacturing process. It is responsible for cutting and shaping the core materials, such as electrical steel, into the required shapes and sizes. The core cutting line consists of various machines, including shearing machines, punching machines, and mitre saws, which work together to produce the core components. The efficiency of the core cutting line directly affects the overall manufacturing process, as any delays or inefficiencies in this stage can lead to increased production time and costs.
Impact of Core Cutting Line Efficiency on Manufacturing Costs
The efficiency of the core cutting line has a significant impact on transformer manufacturing costs. A inefficient core cutting line can lead to increased labor costs, as workers may need to spend more time on each unit to ensure accuracy and quality. Additionally, inefficient core cutting lines can result in increased material waste, as incorrect cuts or shapes may need to be reworked or scrapped. This not only increases material costs but also leads to additional labor costs for rework and scrap handling. Furthermore, an inefficient core cutting line can lead to increased energy costs, as machines may need to run for longer periods to complete tasks, resulting in higher energy consumption.
Factors Affecting Core Cutting Line Efficiency
Several factors can affect the efficiency of the core cutting line, including machine accuracy, maintenance, and operator training. Machine accuracy is critical, as incorrect cuts or shapes can lead to rework and scrap. Regular maintenance is also essential to ensure that machines are running at optimal levels and to prevent breakdowns. Operator training is also crucial, as skilled operators can optimize machine performance and reduce errors. Additionally, the quality of the core materials can also impact the efficiency of the core cutting line, as poor quality materials may require more time and labor to process.
Improving Core Cutting Line Efficiency
To improve core cutting line efficiency, manufacturers can implement several strategies. One approach is to invest in new, high-accuracy machines that can optimize cutting and shaping processes. Additionally, implementing regular maintenance schedules can help prevent breakdowns and ensure machines are running at optimal levels. Providing ongoing operator training can also help to reduce errors and optimize machine performance. Furthermore, manufacturers can also explore new technologies, such as automation and robotics, to improve efficiency and reduce labor costs.
Benefits of Efficient Core Cutting Line
An efficient core cutting line can bring numerous benefits to transformer manufacturers. By reducing labor costs, material waste, and energy consumption, manufacturers can significantly reduce their overall manufacturing costs. Additionally, an efficient core cutting line can also lead to improved product quality, as accurate cuts and shapes can ensure that transformers meet the required specifications. Furthermore, an efficient core cutting line can also enable manufacturers to increase their production capacity, allowing them to meet growing demand and expand their market share.
Conclusion
In conclusion, the efficiency of the core cutting line has a significant impact on transformer manufacturing costs. By understanding the factors that affect core cutting line efficiency and implementing strategies to improve efficiency, manufacturers can reduce labor costs, material waste, and energy consumption. As a result, manufacturers can improve product quality, increase production capacity, and reduce their overall manufacturing costs. As the demand for transformers continues to grow, manufacturers must prioritize core cutting line efficiency to remain competitive and achieve long-term success
- Industry
- Art
- Causes
- Crafts
- Dance
- Drinks
- Film
- Fitness
- Food
- Spiele
- Gardening
- Health
- Home
- Literature
- Music
- Networking
- Other
- Party
- Religion
- Shopping
- Sports
- Theater
- Wellness
- News