How Plastic Injection Molding Supports Complex Geometries
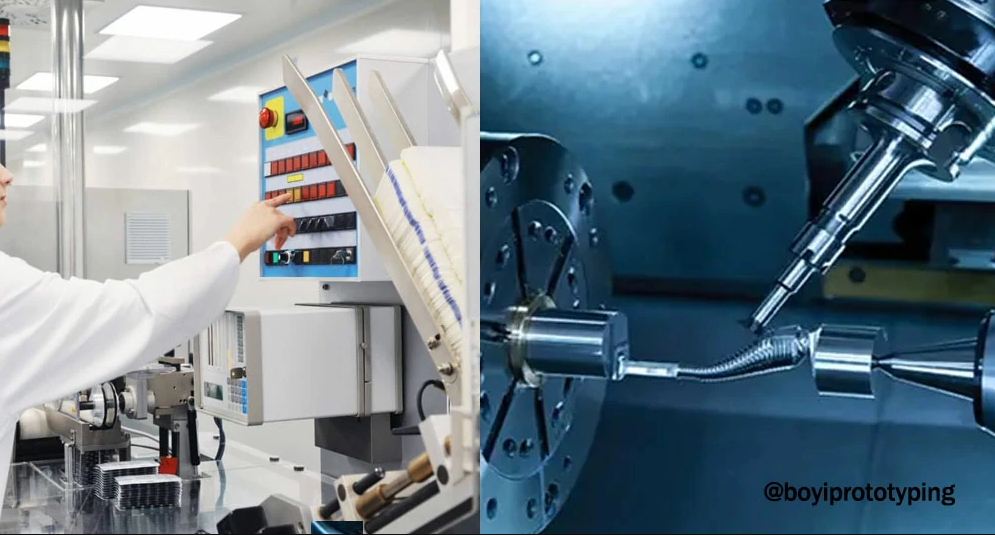
How Plastic Injection Molding Supports Complex Geometries
Plastic injection molding is a versatile manufacturing process that is widely used to produce intricate and complex geometries for a variety of products. One of the main advantages of plastic injection molding is its ability to create intricate shapes and designs that would be difficult or impossible to manufacture using other methods.
One of the key ways that plastic injection molding supports complex geometries is through the use of molds. Molds are custom-designed tools that shape the molten plastic material into the desired form. These molds can be made from a variety of materials, including steel and aluminum, and are precision-engineered to produce highly detailed and complex parts.
In addition to molds, plastic injection molding also makes use of advanced design software that allows engineers and designers to create complex geometries with ease. This software enables the creation of intricate features, such as undercuts, thin walls, and complex shapes, that would be challenging to produce using traditional manufacturing methods.
Another way that plastic injection molding supports complex geometries is through the use of advanced material options. Plastic resins come in a wide range of formulations, each with its own unique properties and characteristics. By selecting the right material for the job, manufacturers can produce parts with specific performance requirements, including strength, flexibility, and heat resistance.
Furthermore, plastic injection molding allows for the production of parts with consistent and precise dimensions. This level of accuracy is essential for ensuring that components fit together properly and function as intended. Whether it's creating intricate medical devices or complex automotive components, plastic injection molding can deliver high-quality parts with tight tolerances.
Additionally, plastic injection molding offers cost-effective solutions for manufacturing complex geometries. By utilizing high-speed and high-volume production capabilities, manufacturers can produce large quantities of parts quickly and efficiently. This not only reduces lead times but also lowers per-unit costs, making plastic injection molding a cost-effective choice for producing complex geometries.
Moreover, plastic injection molding is a highly scalable process that can accommodate a wide range of production volumes. Whether you need a small batch of prototypes or a large-scale production run, plastic injection molding can meet your needs. This flexibility makes it an ideal choice for both low-volume and high-volume manufacturing projects.
In conclusion, plastic injection molding is a versatile and effective manufacturing process that supports the production of complex geometries. This process offers a range of benefits, including the ability to create intricate designs, utilize advanced material options, achieve precise dimensions, and deliver cost-effective solutions. With its ability to produce high-quality parts efficiently and accurately, plastic injection molding is a valuable tool for manufacturers looking to bring their innovative designs to life.
- Industry
- Art
- Causes
- Crafts
- Dance
- Drinks
- Film
- Fitness
- Food
- Giochi
- Gardening
- Health
- Home
- Literature
- Music
- Networking
- Altre informazioni
- Party
- Religion
- Shopping
- Sports
- Theater
- Wellness
- News