You need to pay close attention to the intricacies of the components that are being manufactured by the CNC machining center
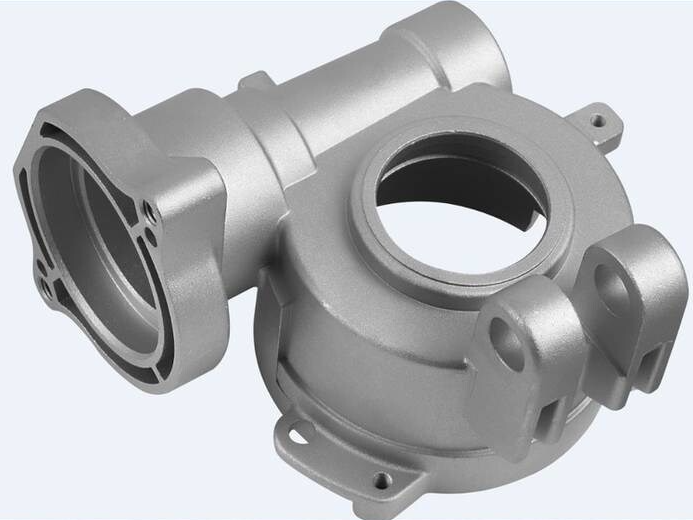
The CNC machining process is highly automated and offers a high degree of flexibility. Processing curved and curved parts with complex contours and shapes, as well as complex boxes and prismatic parts with a large number of holes and grooves, is an area in which it excels. In CNC production of multiple varieties and in small batches, it is utilized. The processing of CNC machine tools can potentially obtain greater economic benefits.
The solution to problems that arise during the large-scale CNC machining process is essentially the same as the solution to problems that arise during regular machining, but it has its own unique characteristics. Therefore, when designing the CNC machining process of parts, it is necessary to follow the CNC machining with good flexibility and a high degree of automation. This type of CNC machining is especially suitable for processing curved and curved parts with complex contours and shapes, as well as complex boxes with a large number of holes and grooves, and prism parts. ,,,,,,,,,,,,,,,,,,Utilizing CNC machine tools can lead to greater economic benefits, particularly in the context of production involving multiple varieties and small batches.
The determination of the tool setting point and the tool changing point of the large CNC machining center, the tool setting point is the starting point of the movement of the tool relative to the workpiece when CNC machining is being done, and the tool changing point is the point at which the tool is changed. The tool setting point is also referred to as the program start point and the tool start point because this is where the execution of the program begins. When programming, the first thing that should be considered is the selection of the tool setting point. When the requirements for machining accuracy of large CNC machining centers are not particularly stringent, CNC manufacturing certain surfaces on the workpiece or fixtures can be used directly as the tool face. On the other hand, when the requirements for machining accuracy are particularly stringent, the tool setting points should be selected as closely as possible to the part's design basis or its process basis. When working with components that are positioned with holes, it is recommended that the axis of the hole be used as the point of reference for setting up the tool.
In order to determine the connection between the machine tool standard system and the coordinate system of the workpiece, the tool setting point needs to have a specific coordinate relationship with the positioning reference of the workpiece. The calculation of the coordinate value ought to be made easier by the selection of the tool setting point, which should also make the tool setting process more convenient. When the tool is being set, the point at which the tool is being set should coincide with the point at which the tool is being positioned. For flat end mills, the so-called tool position point refers to the intersection of the tool axis and the bottom surface of the tool. For ball end mills, it refers to the ball center of the ball head part. For turning tools, it refers to the tool tip. For drill bits, it refers to the drill tip. The so-called tool position point for a wire electrode cutting machine refers to the focus of the wire electrode axis and the part surface. Whenever the tool needs to be changed while the processing is being done, the tool change point should be specified, and the position of the tool change point should be set according to the principle that the workpiece, fixture, and machine tool should not be damaged while the tool is being changed.
The company utilizes computer numerical control (CNC) machining as its primary process, possesses physical factories and testing equipment, and integrates rapid prototyping, mold, post-processing, and other supporting manufacturing resources in order to provide customers with rapid proofing, small and medium-sized batch manufacturing, and trial assembly. This helps customers save a significant amount of worry and effort. services available in a single location. The majority of the metal components that are processed by this company are made of aluminum alloy, stainless steel, copper, and other raw materials. Additionally, the company processes plastic components made of what is stainless steel 304 ABS, PC, POM, PEEK, nylon, and glass fiber. In addition to the expertise that we have in the production of parts made from traditional materials, we also have a great deal of experience in the production of parts made from light alloys and composites.
The widespread use of CNC machining technology has contributed to an ongoing increase in the degree of complexity of the component parts' structures. When it comes to the processing of certain CNC parts, positioning and clamping can be very challenging, and it is not possible to perform multiple positions of positioning and clamping on these parts. Integral machining is a one-step forming technology that forms all of the faces and holes of the part at once. This is accomplished by rotating and flipping the worktable according to the angle on the machine tool of the horizontal or vertical-to-horizontal conversion machining center. The craft handle and the workpiece are separated by the layer milling part's connecting piece, which also serves as the craft handle's connecting piece. When the positioning and clamping processes are repeated twice, the positioning error is significant, and it is difficult to perform the clamping. When the one-time processing forming technology is utilized, the accuracy of the shape and position of the precision parts is well guaranteed after processing. This is because the parts are not unloaded during the processing.
The machining factory makes full use of the multi-angle and all-round processing advantages of the CNC machining center, processes the parts with small deformation by utilizing the high speed and small feed of the carbide milling cutter, and uses the residual part of the profile part as the positioning and pressing process handle. All of these advantages are used in conjunction with one another. The automatic programming function of the UG software guarantees that the entirety of the machined parts are consistent and that they have a good cohesion on all sides.
Install the special bending plate for cnc parts processing on the working turntable of the horizontal machining center near the center of the table using the positioning principle of one side and two pins. Proceed with the processing after positioning a firm sponge pad directly below the part at the point where it will fall. Utilize a 6mm carbide milling cutter to probe into the flat hole of the special bending plate fixture. Set the milling depth of each layer to 0. 1mm, and cut the outer contour of the part R49mm, 86mm, as well as the connection of the residual process handle in layers. This will cause the workpiece to become detached from the residual process handle, and the parts will fall off. The fitter will clean the residual flash that is located around the part R49mm on the hard sponge pad that has been pre-placed.
- Industry
- Art
- Causes
- Crafts
- Dance
- Drinks
- Film
- Fitness
- Food
- Spiele
- Gardening
- Health
- Home
- Literature
- Music
- Networking
- Other
- Party
- Religion
- Shopping
- Sports
- Theater
- Wellness
- News