Key Challenges Facing Automotive Load Floor Market in Design, Cost, Innovation, and Compliance Areas
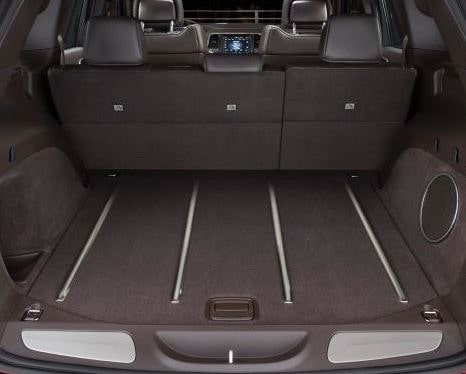
The automotive load floor market is a vital component of vehicle interior systems, enhancing cargo space functionality, safety, and aesthetics. With increasing demand for lightweight materials, innovative storage solutions, and modular design, the market is steadily evolving. However, this transformation is not without its hurdles. The industry faces multiple challenges that can impact its scalability, efficiency, and adaptability in a rapidly changing automotive environment.
This article explores the key challenges currently restraining the growth and innovation of the automotive load floor market.
1. High Cost of Lightweight and Sustainable Materials
One of the most prominent challenges in the automotive load floor market is the high cost of advanced materials. As the industry shifts toward sustainability and weight reduction, manufacturers are adopting materials like thermoplastic composites, recycled plastics, and natural fibers. While these materials provide environmental and performance benefits, they often come at a significantly higher cost compared to traditional plywood or standard plastics.
This increase in cost becomes especially problematic in mass-market or budget vehicle segments, where cost efficiency is crucial. Many manufacturers find it difficult to justify the investment in premium materials without clear consumer demand or regulatory incentives.
2. Design Limitations in Electric and Compact Vehicles
With the rise of electric vehicles (EVs) and compact cars, automotive design is becoming increasingly constrained. Battery placement in EVs often occupies the underfloor area, limiting the available space for traditional load floor structures. This spatial restriction creates challenges in:
-
Designing strong yet thin load floors
-
Integrating underfloor storage compartments
-
Maintaining thermal and fire safety near battery packs
As a result, manufacturers must re-engineer their load floor systems to fit the structural and safety needs of these evolving vehicle platforms, often requiring more R&D and prototyping, which delays market readiness.
3. Complexity in Manufacturing and Customization
Modern vehicles demand customized and modular interior components, including foldable, multi-level, or sliding load floors. While this enhances user convenience and vehicle appeal, it significantly increases production complexity. Multi-component systems require:
-
Precision molding
-
Mechanical integration
-
Additional assembly steps
This complexity adds to manufacturing time, labor costs, and quality control challenges, especially in high-volume production lines. Smaller suppliers without advanced automation struggle to maintain the precision needed, making it harder for them to compete with larger players.
4. Lack of Standardization Across Vehicle Segments
Automotive manufacturers produce a wide range of vehicles—SUVs, hatchbacks, sedans, MPVs, and EVs—each with unique cargo dimensions and structural requirements. As a result, load floor systems often require customization for each model. This lack of standardization:
-
Increases design and tooling costs
-
Limits scalability
-
Reduces the potential for mass production
Standardized solutions are difficult to implement due to varying OEM specifications, and this fragmentation in design requirements limits the market’s ability to benefit from economies of scale.
5. Limited Consumer Awareness and Perceived Value
Despite their functional importance, load floors are not a key decision-making factor for most car buyers. Consumers typically focus on exterior styling, infotainment systems, fuel efficiency, or safety features. This low perceived value limits OEM investment in advanced load floor features unless they are marketed as premium options in high-end models.
The lack of consumer enthusiasm also discourages automakers from exploring new innovations in this space, leading to slower adoption of upgraded materials, smart features, or multifunctional layouts.
6. Evolving Regulatory and Environmental Compliance
Governments and regulatory bodies around the world are increasing pressure on the automotive industry to reduce emissions and improve recyclability. Load floor manufacturers now face challenges in ensuring that their materials and manufacturing processes:
-
Comply with emissions regulations
-
Meet recyclability and eco-certification standards
-
Avoid banned or restricted substances
These evolving requirements can lead to redesigns, production delays, and increased compliance costs. For global manufacturers, meeting different regulations across multiple regions adds another layer of operational complexity.
7. Supply Chain Vulnerabilities and Global Disruptions
Global supply chains have faced major disruptions due to geopolitical tensions, pandemics, and raw material shortages. The automotive load floor market is directly affected by these issues, particularly when it comes to sourcing specific polymers, composites, or adhesives.
Delays in raw material procurement can stall production, increase lead times, and erode customer trust. In some cases, suppliers are forced to switch materials, which can affect product quality, compatibility, or compliance with OEM standards.
8. Integration with Emerging Vehicle Technologies
As the automotive industry embraces smart features and digital integration, there is a growing demand for intelligent interior systems. Load floor solutions that incorporate:
-
Embedded sensors
-
Fold-out storage with electronic locking
-
Weight-detection systems
…are being explored. However, integrating electronics with structural components introduces new challenges such as waterproofing, power supply management, and increased maintenance needs. It also requires collaboration between material engineers, software developers, and OEM designers—something not all suppliers are currently equipped to handle.
Conclusion
The automotive load floor market is navigating a complex environment shaped by rapid technological change, shifting consumer expectations, and strict regulatory requirements. While opportunities for innovation and growth are significant, so too are the challenges.
Addressing these hurdles—ranging from cost and design complexity to supply chain and compliance issues—requires strategic planning, collaborative partnerships, and investment in research and development. Companies that adapt effectively will be better positioned to thrive in an increasingly competitive and transformative automotive ecosystem.
- Industry
- Art
- Causes
- Crafts
- Dance
- Drinks
- Film
- Fitness
- Food
- Jogos
- Gardening
- Health
- Início
- Literature
- Music
- Networking
- Outro
- Party
- Religion
- Shopping
- Sports
- Theater
- Wellness
- News